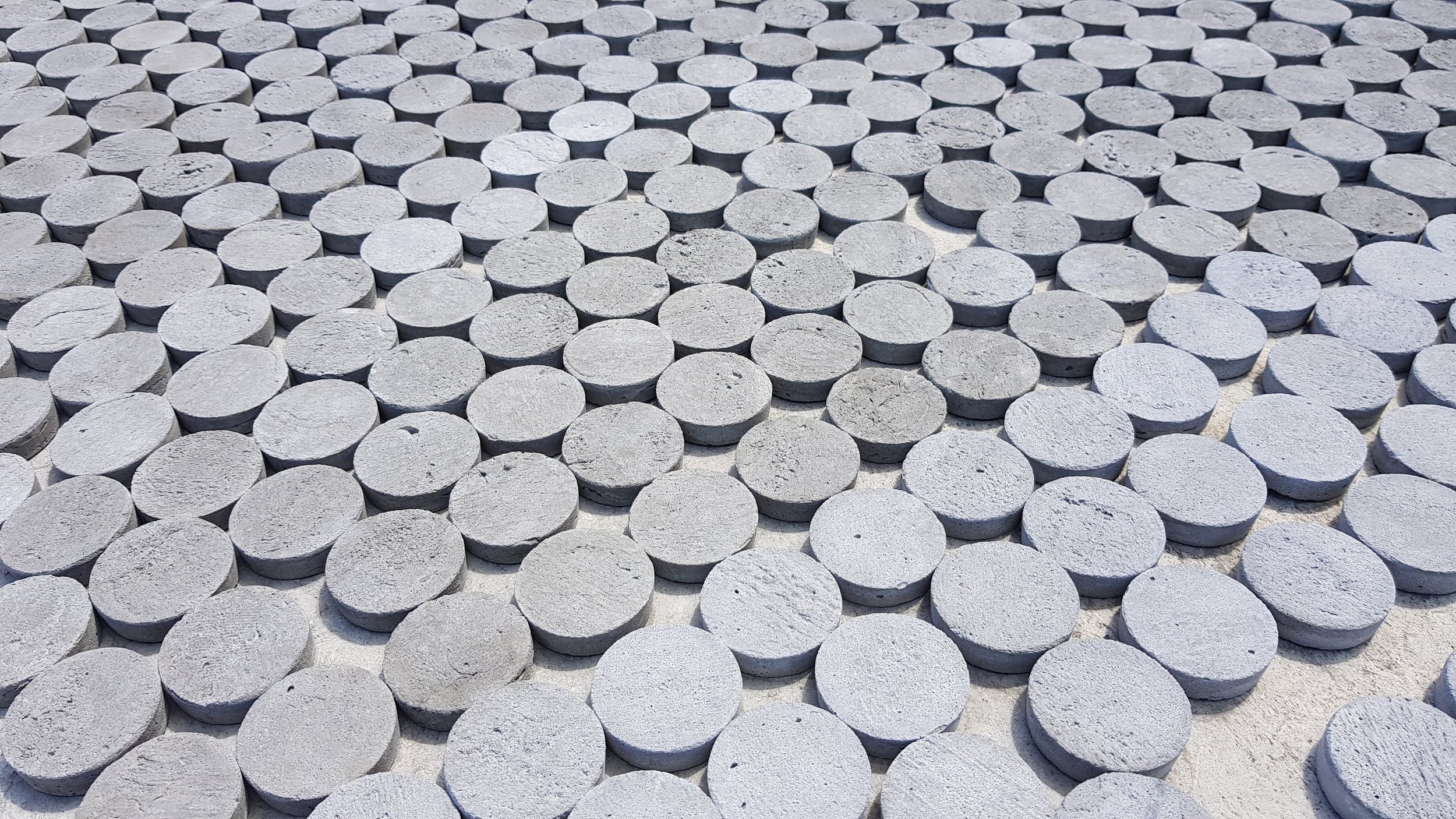
What is GRC
Glassfibre Reinforced Concrete is one of the most versatile building materials available to architects and engineers today.
Glassfibre Reinforce Concrete (GRC or sometimes GFRC) is a composite material comprising a mixture of hydraulic cement, silica sand, alkali resistant (AR) glass fibres and water. The glass fibres in GRC effectively reinforce the mortar mix thereby improving its tensile strength and characteristics. Click here for GRC Technical Information
GRC was developed in the 1960's as a corrosion free alternative to traditional steel reinforced concrete. Initially manufactured as an exterior cladding material, GRC can be moulded into a wide variety of complex shapes, profiles and architectural components. GRC is ideally suited to the popular fast-track approach of using lightweight, prefabricated cladding panels for the exterior of modern buildings.
The main advantage of GRC panels over the corresponding precast concrete alternatives is the considerable saving in weight. This results in savings in the costs of transportation, handling and erection of panels. If this weight advantage is considered at the design stage, it should be possible to affect substantial environmental and economic savings in design of foundations and superstructures for both low and high rise building constructions.
Other notable advantages of GRC cladding are its durability, seismic capabilities, chemical resistance, non-combustibility and good sound/heat insulation properties.
Uses of GRC
The uses of Glassfibre Reinforced Concrete are almost endless and limited only by your imagination. GRC is incredibly versatile and the ability to be flexible in structure, profile and shape will suit any project from innovative, cutting edge designs and artworks to traditional cladding projects or historic restorations.
GRC is primarily used as an exterior facade or cladding material for both new construction and recladding or restoration of existing building facades. GRC cladding panels are generally manufactured by the 'Hand Spray' technique and the skin is bonded to a steel stud frame. The method can produce high-performance materials from which panels with extremely thin, lightweight sections are achievable.
Due to its extreme flexibility, GRC is also the perfect material to create highly detailed and ornate patterns and textures for interior and exterior panels or artworks that don't require backing frames. Architectural dressings for exterior wall, window, spandrel, cornice, column liners, fireplace surrounds and benchtops are also possible.
The low rate of shrinkage of GRC makes it an excellent choice for historic restoration projects. Moulds can be taken from existing building ornaments to recreate their original classical appearance.
GRC can be painted or coloured to almost any colour using a pigment oxide added to the mix at the time of casting.
Benefits of GRC
Durable
The weathering characteristics of GRC are as good as any precast material. Unlike traditional reinforced cement, GRC uses alkali resistant (AR) glass fibres throughout the matrix to provide reinforcement so is not at risk of corrosion and does not require further maintenance.
The GRC can be enhance for greater protection and durability, with a wide range of specialised products available that offer additional resistance to impact, weather, graffiti and water.
Strong and Lightweight
Typically manufactured to a skin thickness of 12mm, GRC can be cast in thinner sections and can be up to 75% lighter than similar pieces of traditional precast concrete.
The reduced weight of panels makes them easier and cheaper to handle with reduced transportation costs, Generally, more GRC panels can be shipped in a single load than traditional precast.
GRC is a high impact strength material with a strength-to-weight ratio superior to most other materials. The glass fibre has a tensile strength 3 to 4 times greater than the equivalent steel fibre. GRC has high compressive and tensile strengths. For more information about the properties of GRC, click here for Technical Information.
GRC panels reduce loadings on foundations and perimeter columns which can lead to significant savings in superstructure and foundations if designed in from concept.
Versatile
GRC offers unrivalled creativity with the ability to accurately reproduce any small or large design, including historic ornaments, ornate patterns and complex shapes.
The material can be finished in a wide variety of textures and colours, giving designers greater control over the surface detail and quality of finish.
Environment
GRC is generally cast in thin skin sections which consume less raw materials and energy during manufacture. Consequently, the reduced weight and thickness of GRC panels can provide significantly lower environmental impacts during transportation to site and during installation.
Technical Information
For typical building cladding panel construction, GRC castings are manufactured by spraying a series of layers of polymer-concrete material with glass fiber reinforcement in a female mould. An engineered steel frame is bonded to the casting, allowing the panels to be installed to a building's structural steel or concrete slab by either bolt fixing or welding.
Typical Range of GRC Properties